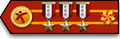
上将
UID2414886
  
U币81
G币30171
技术0
主题37
精华0
阅读权限90
注册时间2015-10-7
最后登录2024-11-21
在线时间2020 小时
居住地浙江省 宁波市 象山县
QQ
手机13285844859
毕业学校宁波高等专科学校
学历专科
自我介绍再苦:也别忘记坚持!再烦:也别忘记微笑!再急:也要注意语气!再累:也要爱自己!低调做人,你会一次比一次优秀!
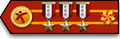
上将
  
 
|
推荐

楼主 |
发表于 2019-11-15 21:10:07
|
只看该作者
所谓模具的适应性是指同一副模具在不同的压铸机上,由不同的人员操作以及在较宽范围内的工艺参数的条件下,生产出合格压铸件的顺利程度而在压铸实际生产过程中,影响压铸件质量的因素较多。诸如:压射压力、压射速度、快压启动位置、熔炉保温温度、模具温度、模具结构等,在这些因素中哪些因素对压铸件的质量影响较大呢?
在压铸生产企业中一个普遍的观点是:模具对压铸件质量的影响占了百分之七十,而内浇口参数对模具的适应性又起着举足轻重的作用。现略举几例说明模具内浇口对模具的“适应性”的影响及处理方式。
一、内浇口截面积对压铸件质量的影响
在一定的压射条件下,内浇口面积过大时,会使填充速度过低,金属过早凝固,甚至导致充填不足;而过小的内浇口面积,会使喷射加剧,增加热量损失,产生涡流并卷入过多的气体,对模具冲刷加剧,导致模具早期报废。
内浇口截面积的大小,常常是凭经验在设计绘图过程中来确定的,单纯地依据经验公式所计算内浇口的截面积,割裂了内浇口截面积与充填速度和充填时间的密切联系,内浇口截面积与充填速度和充填时间之间存在着不能有效匹配的风险,设计结果能在多大的工艺范围内进行修改,设计者并不清楚。个人经验不同得出的内浇口截面积相差悬殊,在实践中就会出现模具适应性差的现象;生产实践中模具内浇口截面积与压铸件不匹配的情况屡见不鲜,当这种不匹配性差距不大时,其表现并不是很明显,在模具使用中,操作人员常常会感到模具不好用;当其差距较大时就会明显的表现出来,压铸件无法成形、废品率高、质量不稳定等。
下面所述是一个真实的生产实例;这是一个桶状的壳体类零件,平均壁厚4.5mm左右;采用的合金为:ADC12, 压铸件重量(包含净重和渣包)4700克,内浇口截面积460mm见附图1。
使用设备:800T压铸机 压射头直径φ110。
主要工艺参数为:浇铸温度650℃、模具温度230℃、快压射行程202mm、快压射手轮开度7圈。
在生产过程中发现压铸件填充不满,表面质量差:废品率高达50%以上:从图1可以看出,这是一个形状比较简单的压铸件。其浇排系统的设计基本上是合理的,一般情况下,上述压铸工艺是能生产出合格产品的。针对出现的质量问题.我们本着先易后难的方针,再次对生产工艺进行了适当的调整但是,基本无效。
为此,我们根据模具和压铸机的参数画出了PQ2图:如图2所示。
从图上发现,生产发生异常的主要原因是内浇口截面积与压射系统不协调引起的。我们知道,对于体积较大的产品,当浇口面积较小时将导致填充时间过长,型腔不能完全填充或填充不满。制品表面出现大面积的冷隔及夹杂着大量的冷料块,整体强度严重下降;这就要求压射系统所能达到的实际填充时间要小于压铸件需要的填充时间,压铸件需要的最长填充时间的计算可参见下式:
T=K×X×1000×(TI-TF+S×Z)/(TF-TD)
其中:T为压铸件需要的最长填充时间,单位ms,K为系数,与所用的模具材料有关,常用模具钢H13的值为0.0346,X为压铸件平均壁厚,单位mm,TI为金属液温度,单位℃,TF为金属液最低流动温度,单位℃,S为目标固体百分率,单位%,Z为固体系数,单位%,TD为模具温度,单位℃。
根据上式计算的充型时间为88.8ms 这是一个与工艺参数、压铸件壁厚相关,而与内浇口截面积无关的经验计算值:由P-Q2计算可知,在内浇1∶3面积为460mm时,该压铸模具和设备所组成的压铸系统所能达到的最小充型时间为86.3ms。显然,这个值与压铸件需要的最长填充时间相差无几,在这种条件下,生产过程中就会对工艺参数要求很高,工艺的略微波动会造成压铸件表面产生各种各样的缺陷,这样的模具如果放到一台性能更高的压铸机上生产也有可能顺利的生产合格的压铸件,但在现有的压铸机上是很难正常生产的。
根据计算,当内浇口面积达到700mm2 时,系统所能达到的最小充型时间为64.9ms,这个值与压铸件需要的最长填充时间相比留有较大的调整空间,这就为压铸工艺的调整留下了充分的余地。这样的模具基本可以适应各种不同性能的压铸设备上生产用修改后的模具试生产,操作人员普遍反映,模具好用了、废品率也下降到了3%左右。
二、内浇口形状对压铸件质量的影响
尽管压铸件内浇口的形状与压铸件的外形有很大的关系。实际设计中更是千差万别,但是参照一些模具设计手册和一些成功的经验数据,一般都能设计出比较合理的内浇口结构。对于各种内浇口的设计,请参阅相关资料,本文不再赘述。下面主要就浇口设计中的局部细节对模具“适应性”的影响加以浅述。
内浇口导向角度对压铸件成型的影响在模具使用中发现,内浇口的导向角对压铸件的填充起着一个至关重要的作用,不恰当的导向角度将会导致模具的“适应性”大大降低 下面以摩托车上常见的一种零件—缓冲体为例加以说明。
该产品采用的合金为:ADC12,压铸件重量(包含净重和渣包)705克,平均壁厚4.3mm,单腔内浇口面积145mm2 ;
使用设备:280T压铸机压射头直径Φ60模具结构为一模两腔,主要工艺参数为:保温温度630℃、模具温度220℃、快压射行程95mm、快压射手轮开度4.5圈。
生产过程中发现在图3所示部位产品油污、夹皮(所谓夹皮是指:压铸件局部出现分层)严重;不同的操作人员生产,废品率相差较大,这就是—个典型的模具“适应性”差的现象;技术熟练的操作人员基本上能正常生产,熟练程度稍差的人员,几乎不能正常生产。
1)从模具填充上分析
从压铸系统的浇道部分可看出,其扇形角度很小,内浇口导向角几乎为零(见图3),金属液进入型腔后就快速的冲击到型腔对面,封闭两侧的两个渣包造成图3所示的局部区域内的空气、脱模剂混和气体等无法正常排出,导致压铸件局部夹皮油污严重。
2 )从人的因素分析
人的因素方面,主要在于脱模剂的喷涂控制,由于压铸生产是采用手工喷涂脱模剂,每个人的经验不同,喷涂差异较大。如果脱模剂喷涂过多,则产生废品,喷涂过少又易发生粘模。由于模具排气不畅,稍微的喷涂差异,就会造成产品报废只有个别技术熟练的操作人员才能进行生产,对脱模剂喷涂量的要求,到了一个近乎苛刻的地步。
根据上述分析,解决问题的思路在于改善缺陷部位的排气;最后决定仍然利用原有的浇排系统,通过改变内浇口的导向角来改进图4。在A处所示部位增加了内浇口的导向角。通过内浇口导向角度的更改,改善了模具的填充质量,提高了模具的“适应性”。
浇口与压铸件本体结合处细节的处理在生产壳类零件时,经常会发生的一个问题是压铸件在内浇口处开裂,造成产品报废。仔细观察压铸件开裂部位会发现,所有的裂纹均是沿着内浇口的前沿向压铸件内部延伸的;其形成的主要原因在于内浇口处的局部尖角所形成的内部应力较大。而浇口的去除,多数是靠敲击去除的,操作人员在去除浇口时,由于浇口处局部受力较大,造成了压铸件开裂。
针对此类开裂问题,可对模具做一个简单的处理,消除局部尖角即可。对模具处理后,压铸件未再发生过类似的问题。
三、结束语
通过上述实例分析,我们可以看出,压铸模具的内浇口设计对于压铸模具的“适应性”的影响是很大的,一个合理的内浇口参数是生产出优质产品、保证模具“适应性”的基础;但同时,内浇口的局部细节的处理不当往往是模具“适应性” 差的重要因素;合理的内浇口设计加上局部细节的优化组合是提高模具“适应性”的有效途径,也是改善产品质量,降低废品率的根本保证。
★ 本文公式说明:这是一个在各种参考资料上都能见到的一个经验公式,公式的计算比较筒单,需要注意的是,公式中s和z的取值是不包含其后面的%的。
|
|