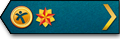
上等兵
UID2124499

U币1
G币65
技术0
主题1
精华0
阅读权限20
注册时间2013-11-28
最后登录2018-1-5
在线时间4 小时
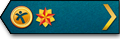
上等兵

|
许多人对拉伸模望而却步,这是因为拉伸模不仅仅设计时要考虑许多因素,更主要的是在试模时往往不能一次成型,还要经过多次修
模,才能达到理想的结果。因此,在实践中不断积累经验,对拉伸模的设计大有裨益。
1.材料:
好的材料是成功的一半,对于拉伸,万万不可忽视。
拉伸用冷轧薄钢板主要有08Al、08、08F、10、15、20号钢,其中用量最大的是08号钢,分为沸腾钢和镇静钢,沸腾钢价格低,表面
质量好,但偏析较严重,有“应变时效”倾向,不适用于对冲压性能要求高外观要求较严格的零件,镇静钢较好,性能均匀但价格较
高,代表牌号为铝镇静钢08Al。
国外钢材用过日本SPCC-SD深冲压钢,其拉伸性能优于08Al。
经验1:当客户对材料的要求不是很苛刻、反复试模达不到要求时,可以换一种材料再试。
2.毛坯尺寸的确定:
形状简单的旋转体拉伸件的毛坯直径在不变薄的拉伸中,材料厚度虽有变化,但基本与原始厚度十分接近,可以根据毛坯面积与拉
伸件面积(若有修边须加上修边余量)相等的原则计算出。
但是,往往拉伸件形状和过程比较复杂,有时还要变薄拉伸,虽然现在有许多三维软件可进行展开料计算,但其精确度不能100%达
到要求。
解决办法:试料。
一个产件要经过多道工序,头道工序一般是落料工序。首先要进行展开料计算,对毛坯的形状和大小有个大概认识,以便确定落料
模的总体尺寸。在模具设计完成后不要加工落料模的凸凹模尺寸。先用线切割加工毛坯(毛坯较大时可用铣床铣后再钳修),经过后续
拉伸工序的反复实验,最终确定了毛坯尺寸,然后再加工落料模的凸凹模。
经验2:倒排工序,先试拉伸模,后加工毛坯的落料刃口尺寸,事倍功半。
3.拉伸系数m
拉伸系数是拉伸工艺计算中的主要工艺参数之一,通常用它来决定拉伸的顺序和次数。
影响拉伸系数m的因数很多,包括材料性能、材料的相对厚度、拉伸方式(指有无压边圈)、拉伸次数、拉伸速度、凸凹模圆角半径
、润滑等。
有关拉伸系数m的计算和选用原则是各种冲压手册中介绍的重点,有推算、查表、计算等许多方法,祥之又祥,我也是按书选择,
并无新鲜的东东,请看书。
经验3:材料的相对厚度、拉伸方式(指有无压边圈)、拉伸次数是不好在修模时调整的,一定要慎重!!最好在选择拉伸系数m时找同
事校一遍。
4.在凹模上涂润滑油,或在薄板上套薄膜袋。
经验4: 遇到拉伸拉裂时,在凹模上涂润滑油(不要在凸模涂),工件靠凹模一面覆0.013--0.018mm的塑料薄膜.
5.工件热处理
在拉伸过程中,工件由于冷塑性变形,产生冷作硬化,使其塑性降低,变形抗力和硬度增大,再加上模具设计不合理,就需要进行
中间退火,以软化金属,恢复塑性。
注意:在一般工艺中中间退火不是必须的,毕竟要增加成本,要在增加工序和增加退火中进行选择,慎用!
退火一般采用低温退火,即再结晶退火。
退火时要注意的事项有两点:脱炭和氧化。这里主要讲讲氧化。工件氧化后有氧化皮,害处有二:使工件有效厚度变薄,增加模具
磨损。
公司条件不具备时,一般采用普通退火,为减少氧化皮产生,退火时要尽可能将炉膛装满,我还用过土办法:
1.工件少时可与其他工件混装(前提:退火工艺参数应基本一致)
2.将工件装在铁盒中焊封后再装炉。为消出氧化皮, 退火后要根据情况进行酸洗处理。
公司条件具备时,可采用氮炉退火,即光亮退火。不细看,几乎和没退火前颜色一样。
经验5: 对付冷作硬化强的金属或在试模中出现拉裂又无其它办法时,增加中间退火工序。
6.补充几点:
1.产品图上的尺寸应尽可能在一侧标注,让人明确是保证外部尺寸还是内腔尺寸,不能同时标注内外型尺寸。他人提供的图纸有此类
问题应与其沟通,能统一则统一,不能统一时要知道该工件的与其它件的装配关系。
2.对最后一道工序,工件尺寸在外,以凹模为主,间隙以减小凸模尺寸取得;工件尺寸在内,以凸模为主,间隙以增大凹模尺寸取得
;
3.凸凹模圆角半径在设计时尽可能采用小的容许值,给后续修模带来方便。
4.判断工件拉裂的原因时可参考:
因材料质量差而产生的裂口多为锯齿状或不规则形状,因工艺、模具而产生的裂口一般比较整齐。
5."多则皱,少则裂”,按此原则调节材料的流动状况,方法有调整压边圈的压力、增加拉深筋、修整凸凹模圆角半径、工件上切工
艺口等。
6.为保证耐磨性和防止拉伸划痕,凸凹模和压边圈必须淬火,必要时可镀硬铬。
铝质易拉罐成形工艺及模具
感谢论坛发贴网友:LIAOYAO
________________________________________
摘要:对罐体拉伸工序、变薄拉伸工序和底部成形工序进行了分析,并对与这些工序相关的模具在设计和制造中存在的若干关键性技术进行了研究。
关键词:易拉罐;成形工艺;模具;变薄拉伸
1 引 言
铝质易拉罐在饮料包装容器中占有相当大的比重。易拉罐的制造融合了冶金、化工、机械、电子、食品等诸多行业的先进技术,成为铝深加工的一个缩影。随着饮料包装市场竞争的不断加剧,对众多制罐企业而言,如何在易拉罐生产中最大限度地减少板料厚度,减轻单罐质量,提高材料利用率,降低生产成本,是企业追求的重要目标。为此,以轻量化(light-weighting)为特征的技术改造和技术创新正在悄然兴起。易拉罐轻量化涉及到许多关键性技术,其中罐体成形工艺和模具技术是十分重要的方面。
2 罐体制造工艺和技术
2.1罐体制造工艺流程 CCB-1A型罐罐体的主要制造工艺流程如下:卷料输送→卷料润滑→落料、拉伸→罐体成形→修边→清洗/烘干→堆垛/卸→涂底色→烘干→彩印→底涂→烘干→内喷涂→内烘干→罐口润滑→缩颈→旋压缩颈。
在工艺流程中,落料、拉伸、罐体成形、修边、缩径、旋压缩径/翻边工序需要模具加工,其中以落料、拉伸和罐体成形工序与模具最为关键,其工艺水平及模具设计制造水平的高低,直接影响易拉罐的质量和生产成本。
2.2罐体制造工艺分析
(1)落料一拉伸复合工序。拉伸时,坯料边缘的材料沿着径向形成杯,因此在塑性流动区域的单元体为双向受压,单向受拉的三向应力状态,如图1所示。由于受凸模圆弧和拉伸凹模圆弧的作用,杯下部壁厚约减薄10%,而杯口增厚约25%。杯转角处的圆弧大小对后续工序(罐体成形)有较大的影响,若控制不好,易产生断罐。因此落料拉伸工序必须考虑以下因素:杯的直径和拉伸比、凸模圆弧、拉伸凹模圆弧、凸、凹模间隙、铝材的机械性能、模具表面的摩擦性能、材料表面的润滑、拉伸速度、突耳率等。突耳的产生主要由2个因素确定:一是金属材料的性能,二是拉伸模具的设计。突耳出现在杯的最高点同时也是最薄点,将会对罐体成形带来影响,造成修边不全,废品率增高。
基于以上分析,确定拉伸工序选择的拉伸比m=36.55%,坯料直径Dp=140.20±0.0lmm,杯直径Dc=88.95mm。
(2)罐体成形工序。
变薄拉伸工艺分析。典型的铝罐拉伸、变薄拉伸过程如图2所示,变薄拉伸过程中受力状况如图3所示。 在拉伸过程中,集中在凹模口内锥形部分的金属是变形区,而传力区则为通过凹模后的筒壁及壳体底部。在变形区,材料处于轴向受拉、切向受压、径向受压的三向应力状态,金属在三向应力的作用下,晶粒细化,强度增加,伴有加工硬化的产生。在传力区,各部分材料受力状况是不相同的,其中位于凸模圆角区域的金属受力情况最为恶劣,其在轴向、切向两向受拉,径向受压,因而材料的减薄趋势严重,金属易从此处发生断裂,从而导致拉伸失败。比较变形区和传力区金属的应力状态可知:变薄拉伸工艺能否顺利进行主要取决于拉伸凸模圆角部位的金属所受拉应力的大小,当拉应力超过材料强度极限时就会引起断裂,否则拉伸工艺可以顺利进行。因此,减小拉伸过程中的拉应力成为保证拉伸顺利进行的关键。
变薄拉伸拉伸比的选择为:再拉伸:25.7%,第1次变薄拉伸:20%~25%,第2次变薄拉伸:23%~28%,第3次变薄拉伸:35%~40%。
在成形过程中,影响金属内部所受拉应力大小的因素很多,其中凹模锥角。的取值直接关系到变形区金属的流动特性,进而影响拉伸所需成形力的大小,所以,其数值合理与否对工艺的实施有着重要影响。当α较小时,变形区的范围比较大,金属易于流动,网格的畸变小。随着α的增大,变形区的范围减小,金属的变形集中,流动阻力增大,网格歧变严重。而且,随着凹模锥角的增大,变形区材料的应变相应增加,这说明凹模锥角较大时,不仅金属的变形范围集中,而且变形量迅速上升,因而使得变形区金属的加工硬化现象加剧,导致金属内部的应力上升,从而对拉伸产生不利影响。另一方面,在α过于大或过小时都会引起拉伸力的增加,其原因在于:当α过大时,金属流动急剧,材料的加工硬化效应显著,并且随着锥角的增大,凹模锥面部分产生的阻碍金属流动的分力加大,因而所需拉伸力增加;当。过小时,虽然金属流动的转折小,但由于变形区金属与凹面的接触锥面长,锥面上总摩擦阻力大,因此网格畸变虽小,总拉伸力却增大。
由此可见,凹模锥角的合理确定应同时考虑变形区材料的变形特点以及模具与工件间的摩擦状况,凹模锥角合理范围的确定对拉伸工艺有着直接的影响。工艺试验表明,对于CCB-1A型罐用铝材3104H19,其凹模锥角合理取值在α=5°-8°为宜。
底部成形工艺分析。罐底部成形发生在凸模行程的终点,采用的是反向再拉伸工艺。图4为罐底成形受力状况示意图,底部成形力主要取决于摩擦力的性质以及压边力的大小。通常,材料的厚度和强度是一对矛盾,材料愈薄,强度愈低,因此轻量化技术要求减少罐底直径及设计特殊的罐底形状。工艺试验表明,罐底沟外壁夹角若α1大于40°,将大大减小罐底耐压。考虑到金属的成形性,凸模圆弧R不能小于3倍的料厚。但R太大,将会减小强度。球面和罐底沟内壁圆弧R1,至少为3倍料厚,通常R1取4~5倍料厚。减小罐底沟内壁夹角α2,将增加强度,生产中大多数采用10°以下。
罐底部有两处失效点:一为底部球面;二为连接球面和侧壁的罐底部圆弧R。罐底球面的强度取决于以下几个因素:材料的弹性模量、底部直径、材料的强度、球面半径以及在底部成形时金属的变薄程度。罐底球面半径常用公式R球=d1/0.77确定,实际取R球=45.72mm
3模具设计与制造
3.1罐体拉伸模
罐体拉伸过程实际上是筒形件的拉伸过程,拉伸过程中,其材料的凸缘部分在压应力作用下易失稳,导致起皱,因此必须考虑设置防止起皱的压边装置。当材料通过凹模时,凹模圆角部分是一个过渡区,其变形较复杂,除了径向拉伸与切向压缩外,还受弯曲作用,因此凹模圆角选择尤为重要。材料通过凹模圆角后,处于拉伸状态,由于拉伸力来自凸模压力,是经过凸模圆角处传递的,凸模圆角处的材料变薄最严重,此处成为最易破裂的危险断面。
落料一拉伸组合模结构如图5所示。
(1)模具材料:凸、凹模均选择镶硬质合金的材料。
(2)变形量:在易拉罐行业内,一般采用拉伸比δ表示变形量,δn=(dn-1-dn)/dn-1×100%,按此公式,计算如下:
首次拉伸取δ1=(d0-d1)/d0×100%=(140.2001-88.951)/140.2004×100%=36.6%。
再拉伸取δ2=(d1-d2)/d1×100%=(88.951-66.015)/88.951×100%=25.8%。 一般要求2次总拉伸比δ≤64%,δ1≥δ2≥……≥δn,δ1≤40%。
(3)压边装置:采用波形压边圈,0.2-0.3MPa压缩空气作为动力源。
(4)拉伸模工作部参数:
圆角半径:拉伸凹模圆角半径rA取3.556mm,再拉伸凹模圆角半径rA取1.78mm。拉伸凸模圆角半径rB取2.921mm,再拉伸凸模圆角半径取rB2.286mm。
间隙:
拉伸模凸、凹模单边间隙Z/2大,则摩擦小,能减少拉伸力,但间隙大,精度不易控制;拉伸模凸、凹模单边间隙Z/2小,则摩擦大,增加拉伸力。
单边间隙Z/2可按以下公式计算:
Z/2=tmax+Kt
式中 tmax--最大料厚,取0.285+0.005mm
t--公称料厚,取0.285mm
K--系数,当t<0.4mm时,取0.08
则Z/2=0.290+0.08×0.285=0.313mm。
3.2变薄拉伸模 易拉罐罐体成形实际上是将再拉伸和3道变薄拉伸组合在一起的组合工序。现将变薄拉伸模的设计介绍如下:
(1)模具材料。凸模:基体材料为合金工具钢,凸模材料为M2,热处理硬度60~62HRC,镀TiN。凹模(变薄拉伸环):基体材料为合金工具钢,模口材料为硬质合金(牌号为VALENITEVCID-H.L.D或KE-84KENNAMETAL)。
(2)变形量。变薄拉伸比方的计算公式为:δ=(tn-tn-1)/tn×100%,其中tn、tn-1分别为n次及n-1次变薄拉伸后的零件侧面壁厚,计算得:δ1=(0.285-0.225)/0.285×100%=21.05%;δ2=(0.225-0.170)/0.225×100%=24.44%;δ3=(0.170-0.106)/0.170×100%=37.65%。
制罐工厂常常根据给定的材料厚度、罐体厚、薄壁要求、拉伸环和凸模尺寸、拉伸机精度等条件,编制拉伸环和凸模的匹配表供技术人员、模具维修人员和操作人员选配凸模和拉环。
(3)模具的工作部分参数。凸模:凸模圆弧R1.016±0.025mm,再拉伸凸模圆弧R2.286mm,罐底沟外侧壁圆弧R10.478±0.013mm。变薄拉伸环:凹模锥角α=5°,工作带宽度h=0.38+0.25mm。
3.3罐底成形模
罐底成形模结构如图6所示。
罐底凸模材料选用合金工具钢Crl2MoV,热处理硬度60~64HRC,其轮廓形状应与罐型设计一致。底压边模材料选用合金工具钢Cr5MoV,热处理硬度58~60HRC,其轮廓形状应与凸模相匹配。
4 结束语
(1)拉伸工序考虑的重要因素有:拉伸比、凸、凹模圆弧半径、凸、凹模间隙、铝材机械性能、润滑、作业参数。
(2)变薄拉伸工序中凹模锥角。的大小关系到变形区金属的流动性质、应力大小以及模具的受力情况,合理的取值范围为α=5°-8°。
(3)合适的罐型设计是轻量化技术能否实施的关键。研究表明,对于CCB-1A型罐,设计参数选择:底沟外壁夹角α1=32°,罐底沟内壁夹角α2=5°,凸模圆弧R=1.016mm,球面和罐底沟内壁圆弧R1=1.524mm,罐底球面半径R球=45.72mm,可以大大增加罐体强度。
________________________________________
第 1 2 3 4 5 6 7 8 9 10 11 12 13 14 15 篇
下一篇;深冷处理在瓷砖模具上的应用
磁研磨法在自由曲面模具型腔抛光中的应用
来 原:模具制造
________________________________________
鞍山科技大学机械制造与自动化学院(辽宁鞍山, 114044) 陈燕
[摘要] 用电火花加工或用三维自动机床加工出来的复杂自由曲面,在去毛刺、抛光等处理过程中,目前很多企业还停留在费工、费时的手工操作阶段,不仅加工效率不高,自动化程度低,有些甚至无法加工。磁研磨加工法无疑可以弥补其不足.起到改善工作条件,推动自动化进程的作用,加工过去传统工艺所无法加上的复杂形状内表面(如复杂型腔、微型内螺纹表面、弯管内表面等)工件。本文就利用磁研磨法对复杂自由曲面型腔抛光的工作原理以及加工条件等做一介绍。
关键词 磁研磨 型腔 抛先 磁力线 磁场强度
1 磁研磨法的加工原理
作为模具型腔加工最后一道工序的光整加工,其所得到的表面粗糙度值,将直接影响产品的加工质量。由于很多模具型腔表面形状复杂,一般工具难于介入,用传统工艺很难得到理想的表面粗糙度值。目前还没有一套比较成熟的自动化加工方法和工艺来解决这一难题。磁研唐加工法㈥其具有很好的柔性、自适应性、可控性等优点,可以在复杂形状工件表面得到较低的粗糙度值,因而近几年得到国际上广泛的关注。
所谓磁研磨法,就是通过磁场中磁力的作用,将磁性研磨粒子(能被磁铁吸引,并能研磨工件的粉末)吸压在工件表面,工件表面与磁极之间可以有数毫米间隙,磁性研磨粒子在加工间隙中沿磁力线整齐排列,形成磁性刷,并由于磁力的作用压附在工件表面。旋转磁场或旋转工件使磁性刷与工件表面产生相对运动,从而完成对工件表面的研磨加工。
磁研磨加工法的特点是:加工间隙中的研磨粒子组成磁性刷,随着工件形状的变化而变化,在下件表面仿形压附、翻滚、分离,不受表面形状的限制,有很好的加工柔性,可以对任意形状的表面进行抛光处理。另一个特点就是:由于磁力线象x射线一样能够穿过物体,所以,磁性研磨粒子可以进入普通刀具无法介入的任意形状的内部表面,如模具型腔、弯管内部、小瓶颈容器等。通过变化外部的磁铁改变磁力线的方向即可控制磁性研磨粒子按照规定的轨迹研磨内表面,完成过去所无法加工的领域。
2 加工装置的组成
磁研磨加工装置基本上是由能使磁铁和磁性研磨粒子转动并给予一定圆周速度的驱动系统组成。它可以在普通机床上稍加改装即可容易实现。图1是在三坐标数控铣床上,利用磁研磨原理对复杂形状型腔表面抛光加工的示意图。先用该铣床粗加工出三维曲面,然后再用该铣床直接进行磁力研磨精密抛光处理,这样就可以利用加工时的NC数据进行磁研磨加工,从而在精密抛光的同时,保证了工件的形状精度。
装臂中,线圈中的磁极与机床的旋转中心同心.磁极底部与工件之间留有数毫米(1-3mm)的间隙,在间隙中填充磁性磨料。由于磁力的作用,磨料被磁化,磨料沿着磁力线的方向象珠子一样排列,形成具有一定刚度的磁力刷,并对工件表面产生一定的压力,仿照工件表面形状贴附在工件的表面,并伴随磁极在工件表面移动,对表面进行研磨抛光加工。
由于有数毫米的间隙,即使工件表面上有许多凸凹面,磁性磨粒也能随其形状的变化而变化,确保得到精密研磨。因此,即使工件的表面是复杂的自由表面,只要通过控制机床本身一定程度的运动轨迹,即可使复杂的自由表面得以精密研磨抛光,使得原来用普通的砂轮磨削所无法加工的表面,得到很好的精密加工处理,如图2所示。
3 影响研磨特性的因素分析
影响到磁研磨的加工效率和质量的因素很多,磁力的大小是影响到研磨效率的最主要的因素之一。
|
|